Modular Construction: A Compelling Option for the 2032 Athletes Village?
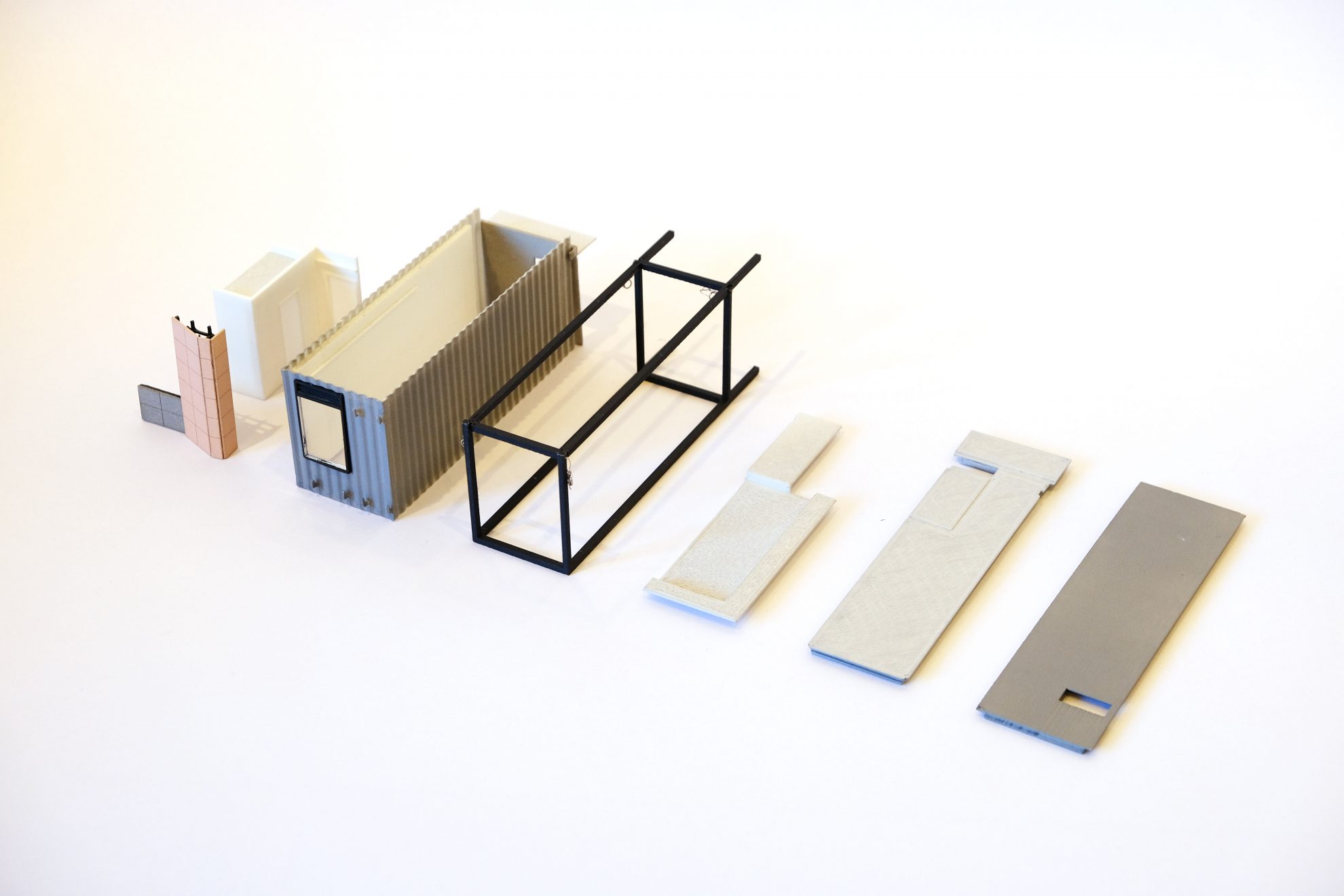
The announcement of the $87 million Northshore Brisbane Street Renewal Program, enabled by Economic Development Queensland, will pave the way for the highly anticipated Brisbane Athletes Village. Brisbane 2032 will require accommodation for some 16,000 athletes and officials during the Olympic Games and around 8,000 during the Paralympics.
If Brisbane wants to truly leverage this once-in-a-generation opportunity to create an enduring legacy, we will have to build more intelligently and efficiently.
In parallel to the preparations for Brisbane’s Olympic moment and the many projects required to deliver a successful Games, there is already significant investment in the city with many large-scale construction projects including Cross River Rail, Brisbane Metro, Queens Wharf Brisbane, and the Queensland Health Big Build hospital expansion program already absorbing much of the construction labour market.
Whilst these projects will contribute to Queensland’s prosperity, the betterment of the state, and help serve the anticipated tourism influx, the reality is, the Australian construction sector is under immense pressure, experiencing a concerning decline in productivity in recent years. Overall, Australia’s labour productivity fell by 3.7% in 2022/23, according to the Australian Productivity Commission’s 2024 Productivity Bulletin. In April, BuildSkills Australia also estimated that an additional 90,000 workers are needed to meet the Housing Accord target of 1.2 million new homes over five years from 2024.
This shortage is particularly pronounced in Queensland. Here, we must not only meet the demands of new projects directly or indirectly driven by the Olympics, but also the acute underlying shortage of housing. Rob Sobyra, Head of Research at BuildSkills said Australia needed to increase the number of workers in residential construction nationwide from 590,000 to 680,000 to meet federal, state and territory governments’ goals for housing. He also said that modelling by BuildSkills suggested demands on the broader construction sector would produce a 40 percent shortfall in labour by 2040.
Benefits of Modular Construction
When considering the learnings from the past three Olympiads, and the constraints and challenges faced by the Queensland construction context, the idea of modular and prefabricated construction is arguably an attractive option for the Brisbane Athletes Village. It addresses the demand for quick and reliable construction, whilst limiting additional pressures on the already crippling labour market. A large percentage of the labour required could move from a site-based context to a factory-style environment.
In March this year, Building Ministers across the country agreed to work together to cut red tape and enable further expansion and growth in Australia’s prefabricated and modular construction industry. In June this year, the Queensland Government also announced that $2.8 billion of the upcoming 2024-25 state Budget has been allocated to the delivery of its housing plan. Part of this funding would support up to 600 more modular homes by the end of 2024.
Development of the Brisbane 2032 Athletes Village could take advantage of an opportunity to boost the uptake of modular construction while public and government sentiment increasingly favours this innovative building method. The 2032 Games may then leave a ‘legacy industry’ for Queensland which might address on-going housing needs and boost the economy for decades to come.
COX Director, Felipe Miranda
Designing great places to live is at the heart of what we do, but we also need to deliver housing faster. The Olympic challenge has historically forced architects to innovate and modular construction in housing is the logical next step.
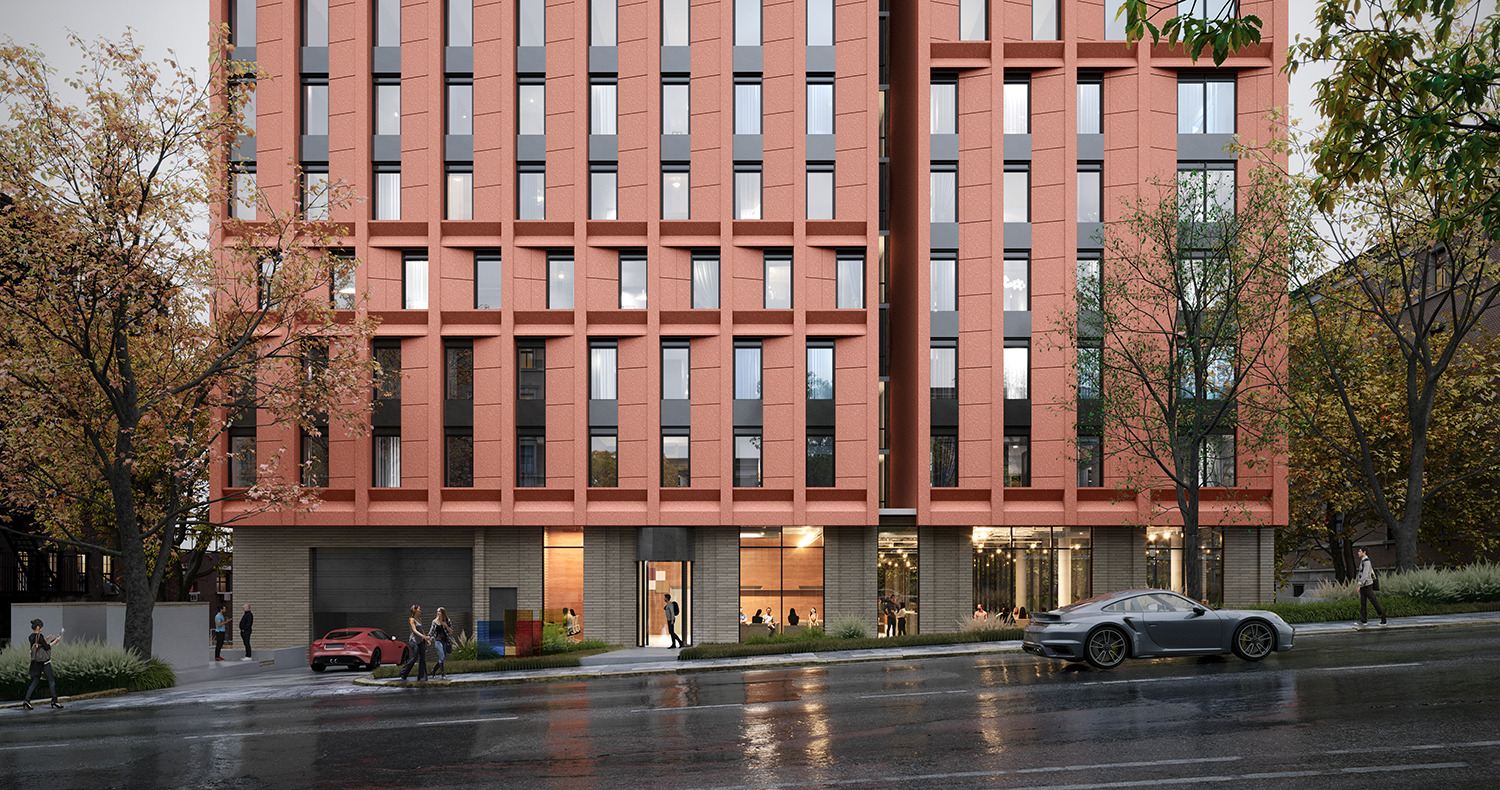
Modular construction operates on the paradigm of ‘Build Off-Site, Assemble On-Site,’ offering substantial time-saving advantages. The bulk of the labour is done off-site in factories, meaning on-site work can be simplified and streamlined into a process of assembly and minor adjustments as needed.
Traditional construction methods typically follow a sequential process, where site preparation, foundation laying, structural framing, and finishing work occur one after the other, with a typical timeline spanning 13-18 months. Modular construction revolutionises this approach by allowing multiple phases of the building process to happen simultaneously, condensing that timeline to approximately 5-6 months.
The prefabricated units (or modules) can be customised to meet specific project requirements and can be easily expanded or modified. Entire prefabricated units, including all finishes and fittings, can be removed from the main super-structure for future reuse, relocation, or repurposing, which presents the significant advantage of adaptability and reusability. This makes modular construction ideal for a wide range of applications, from residential homes and apartment complexes to schools, hospitals, and commercial buildings. Post-Brisbane 2032, the Brisbane Athletes Village can quickly be adapted for any of these applications, with modifications able to be made on-site.
Modular construction can also improve the sustainability of a project. The repetition of prefabricated elements helps to minimise material waste and tighten the loop for possible recycling, contributing to a more accurate assessment of materials and their associated energy costs, empowering better decision making against sustainability metrics. It allows construction with minimum on-site congestion, waste generation and pollution by moving away from a labour-oriented onsite operation to a more process-oriented offsite manufacturing and assembly process.
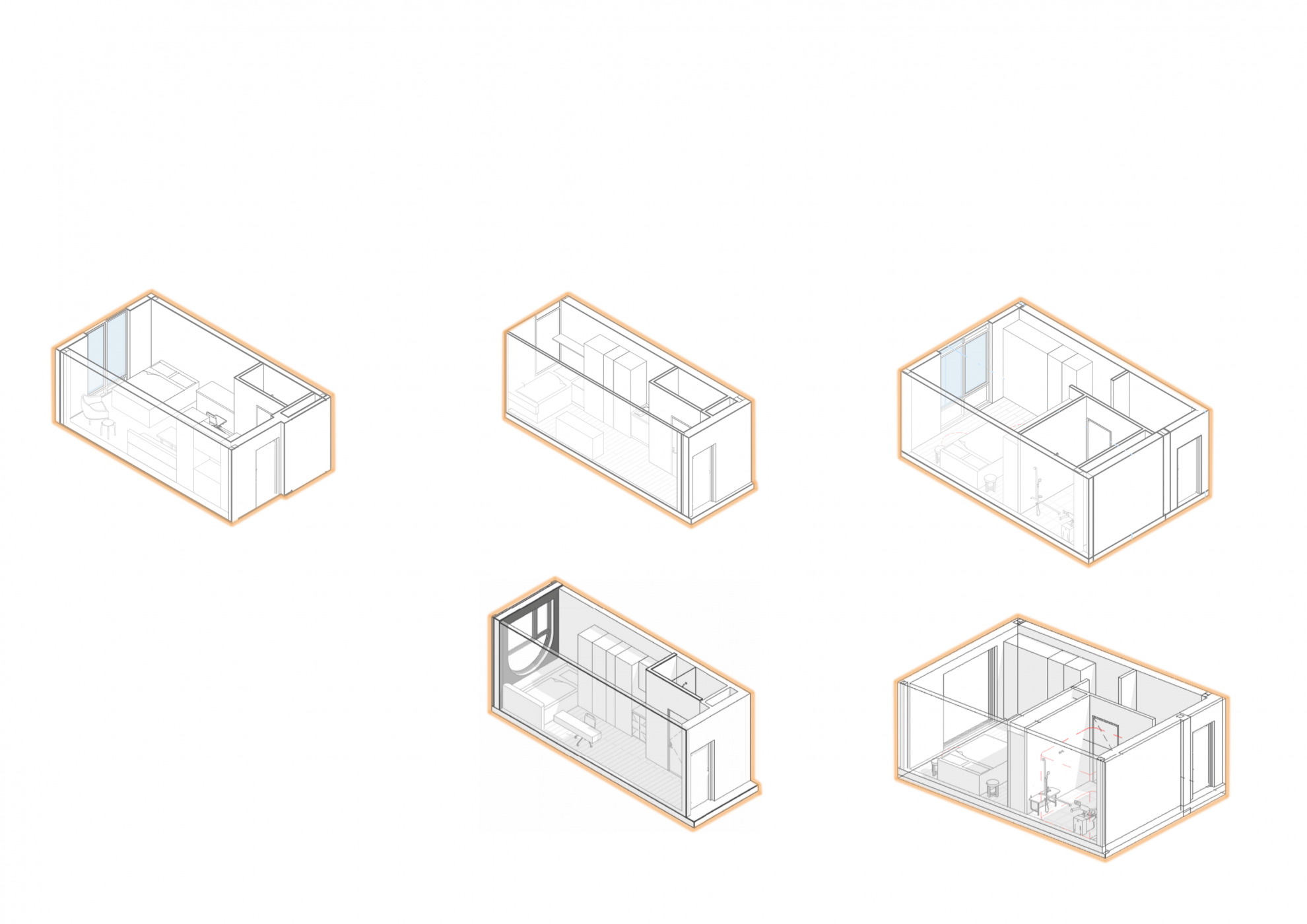
A Step into the Past
Athletes Villages in recent years have experimented with modular construction to varying degrees. Sydney 2000 village was a successful example of a blended model. The developers began construction on the solar suburb of Newington with the goal of it becoming permanent housing, brought in nearly 300 additional modular units, temporarily transformed the site into the Athletes Village for the duration of the Games, and then completed the housing project once the Games ended. The modular units were then deconstructed, relocated, and repurposed as holiday villas which are largely still occupied today.
More recently, it is suggested that some 45 percent of the Paris Athletes Village is made from timber, with a large proportion prefabricated and installed on-site. Examples of prefabricated elements include selected bathrooms, low-carbon concrete floors, load-bearing floor and roof elements, and timber façade and window frames over a concrete structure. “As the installation is fast, nuisance and disruption can be eliminated. Quick element installation also speeds up the overall construction process, reducing the risk of bad weather during the construction phase,” noted the project team behind the Athletes Village.
Reflecting further back in time, pandemic-delayed Tokyo 2020 used modular construction for their aptly named ‘Fever Clinic’, a prefabricated complex of isolation rooms inside the sprawling Village on Tokyo Bay. The London Athletes Village also experimented in this space, using modular concrete cladding panels that were assembled off-site and framed with pre-installed windows, before being craned onto site and re-assembled.
Leaving a Legacy
To ensure Brisbane leaves a memorable Olympic legacy, it is crucial to adopt strategies and solutions that respond to local challenges, community needs, and the city’s long-term aspirations. The Modular Building Institute predicts that nearly 10 percent or around $15 billion of the total construction industry in Australia could be prefabricated within five years.
Given this predicted growth and the successful blueprints that emerged from legacy Olympic Games, the Brisbane Athletes Village could put Queensland at the forefront of high-density modular construction. This is an exciting time for the state and a great opportunity to position us as leaders of Australia’s built environment.

Making Modular Possible with Herring Road
COX has embraced modular construction in its design of Herring Road, a 20-storey student accommodation tower containing over 500 units.
Herring Road prioritises verticality and densification to offer a range of housing options as affordable rentals.
The design handles the requirements for various unit types within the constraints of modular construction, and balances efficient layouts with generous communal spaces. The units are designed for compactness, standardisation, simplification, and domestic comfort.
A mid-tower rooftop terrace adjoins a full floor of communal activity, while at the ground plane a double height space blurs the boundaries between resident amenity, a public café, and an outdoor courtyard.
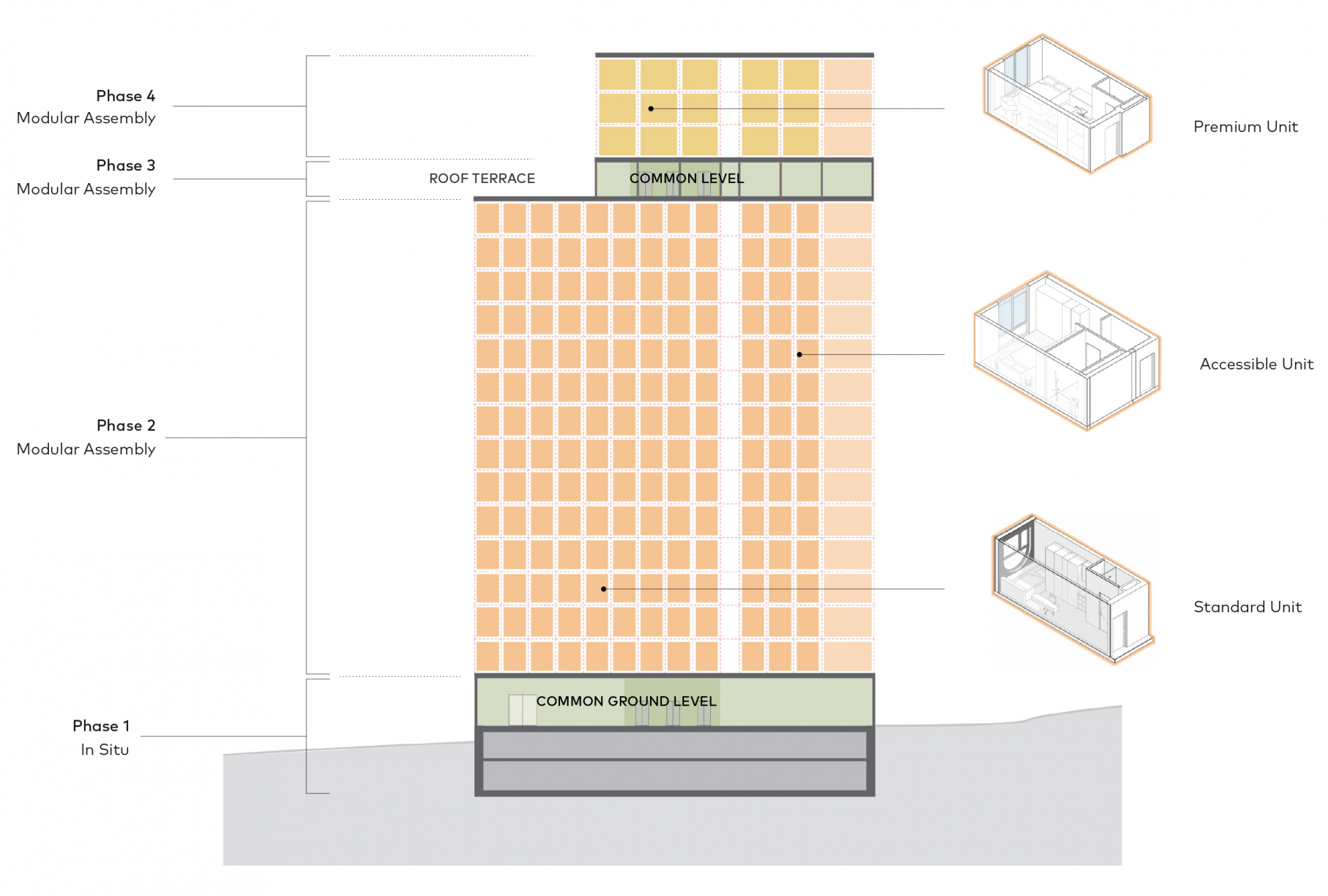
Each module is fully equipped and weatherproofed off-site, complete with high performance glazing (to optimise daylight and views), louvres (for natural ventilation) and services, before being arranged on-site. Additionally, prefabricated rainscreen panels fitted with solar shading elements designed for each orientation, are added on-site to enhance the building’s environmental responsiveness. Initial data suggests modular construction can potentially reduce the construction timeline by one-third and as with any commercial endeavour, time equals cost. Additionally, the modules are designed for disassembly and ease of replacement, extending the lifecycle of the overall building.
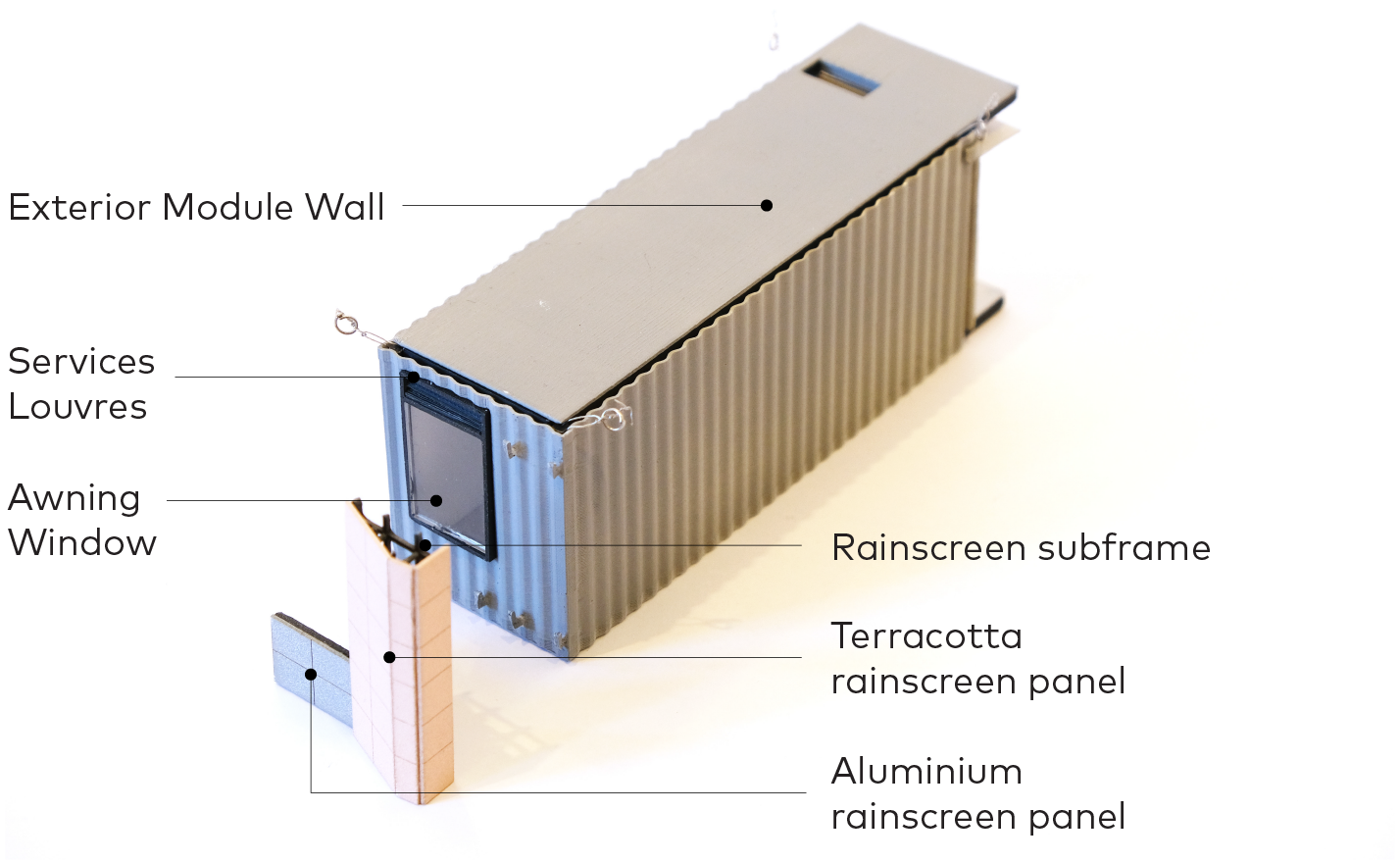
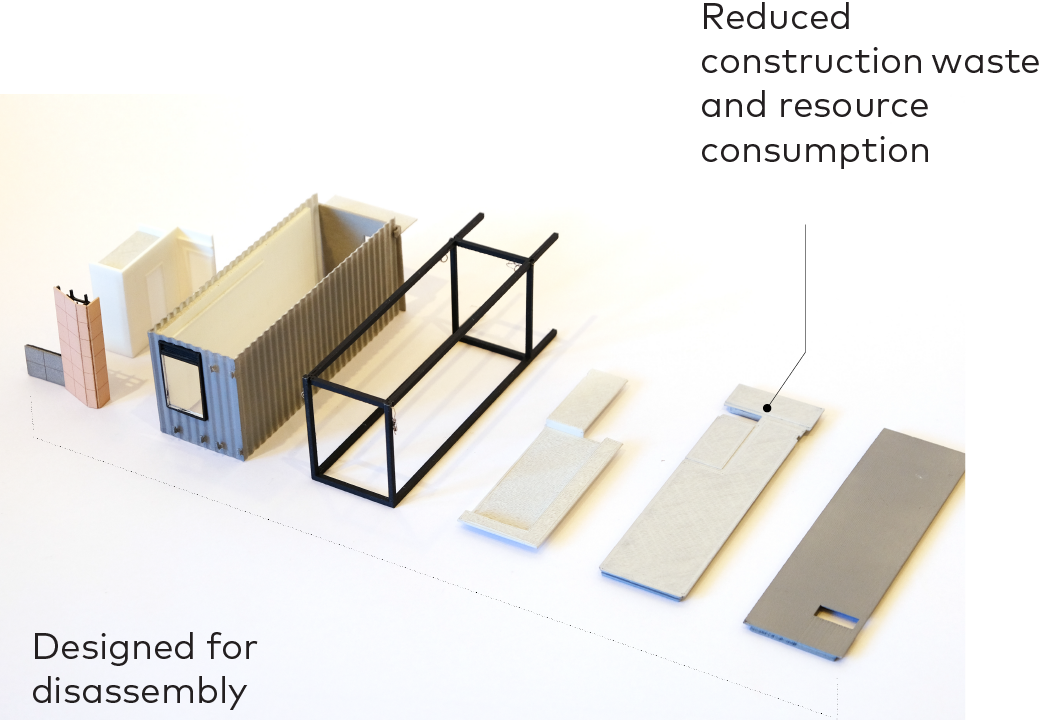